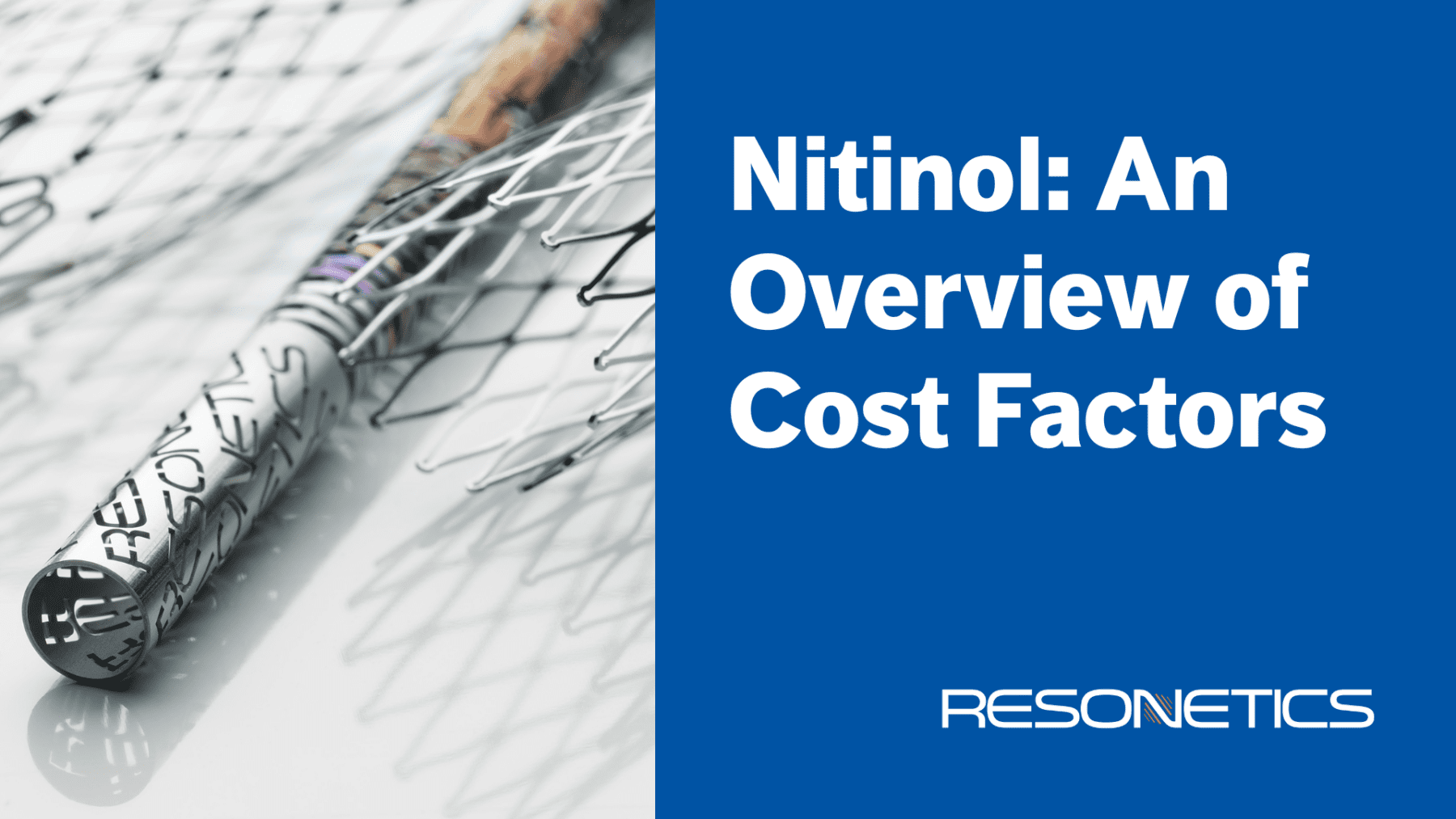
Nitinol is a premium material in the MedTech space, valued for its unique performance characteristics. Nitinol’s cost is influenced by a wide range of factors, from raw material pricing to complex manufacturing processes. In this blog, we’ll explore all the key factors to consider when deciding whether nitinol is the right fit for your project.
Nitinol, a fused nickel-titanium alloy (NiTi), is prized for a number of its valuable properties—many of which make it an ideal candidate for use in medical devices.
For example, nitinol has shape memory, which means it can deform under stress and recover its original shape when the stress is removed or when it is heated. This return to the programmed shape is called superelasticity and is a key feature of nitinol. It’s also corrosion-resistant inside the human body. All of these characteristics make it especially well-suited for tools like stents, guidewires, and catheter components.
But, while this shape memory alloy brings some impressive advantages to the table, its cost can vary. Below, we’ll break down some key factors so readers can make an informed decision when sourcing the best price for this versatile material.
What Affects the Cost of Nitinol?
Clearly, nitinol is far from a “one-size-fits-all” material, and that variation is reflected in its cost.
Several elements can influence cost, including but not limited to the following:
- The cost of titanium
- The form of nitinol required
- Production and processing complexity
- Its heat sensitivity
In recent years, there’s been a rising demand for nitinol—especially in the medical field— due to factors such as the increased adoption of minimally invasive procedures and MedTech advancements.
Material cost of titanium
As you can imagine, raw materials like titanium play a considerable role in the production of nitinol. Titanium is one of the two core ingredients in nitinol, but it’s costly due to the multi-stage process for extraction and refinement. So when prices spike, sourcing, manufacturing, and processing budgets are directly impacted.
Forms of nitinol
Nitinol is produced in several different forms, each designed for specific use cases. Depending on the application, it might take the form of wire, tubing, sheets, or even powder.
- Wire is the workhorse form, used in things like guidewires and stents that require flexibility and consistency.
- Tubing is better suited for structural components, like catheter shafts or implants, where the stability and integrity of its shape matter more.
- Sheets are often used for prototyping or broader, flat components like custom orthopedic staples.
- Powder is mostly for additive manufacturing and niche applications—it tends to be harder to work with and generally more expensive to produce and is primarily used in academic research.
In general, powder and tubing tend to cost more because they require more steps to get right. Wire and sheet are often more economical, though tolerances and specifications can shift costs in either direction.
(Learn More: Download our brochure on Nitinol Materials)
Processing nitinol
Nitinol can “take orders” well. But making it do exactly what you want during activation isn’t always so straightforward.
It takes a high level of control—tight tolerances, precise temperatures, and often custom tooling—to shape it into a finished component. Whether you’re cutting, forming, or doing a finishing process, every step requires careful handling to preserve the alloy’s unique properties.
Nitinol processing can involve anything from ultrafast laser cutting to electropolishing, shape setting, and braiding—each step adding time, expertise, and cost. Shape setting, for example, demands exact temperature control to lock in performance characteristics. Electropolishing improves the surface finish and biocompatibility but adds another stage to the process. Even the way wire is processed can vary depending on the supplier, affecting not just how it performs, but also how much it costs to process.
Nitinol’s heat sensitivity
Nitinol’s properties make it powerful but also fragile. The same thermal responsiveness that gives it shape memory can also easily lead to deformation caused by improper heat during manufacturing, storage, or transport.
For manufacturers working with tight tolerances, even minor temperature shifts during transit can cause problems. If nitinol is exposed to the wrong level of heat at the wrong time, it can lose its shape-setting precision—or worse, behave unpredictably in the field. That risk often means using specialized packaging or controlled shipping methods to keep the material stable end-to-end.
Nitinol’s increasing importance in MedTech
Nitinol has long been valued for its unique properties—shape memory, superelasticity, and biocompatibility—but it’s now taking more of a key role in MedTech. Once used primarily in niche applications, this specialty alloy is becoming a cornerstone of modern medical device design.
As the healthcare industry moves steadily toward minimally invasive, high-precision procedures, demand for materials that can flex, recover, and perform reliably under stress is accelerating. Nitinol checks every box, making it the material of choice for applications like stents, guidewires, and other critical components.
Download Our Nitinol Whitepaper
The cost of working with nitinol isn’t tied to any one factor but a combination of several factors. From the form it takes to how it’s processed, how it handles heat, and even the fluctuating price of titanium, each variable plays a role.
If you’re looking for a deeper dive into how nitinol works and why its durability remains in such high demand, check out our latest whitepaper on nitinol.
Have questions or need help with a specific project? Talk with our team here.